In het Limburgse Lomm staat het specialiteitenbedrijf van aardappelverwerker Aviko. Met de nieuwe vriesinstallatie van Equans vriest Aviko daar nu per vrieslijn elk uur 10 ton friet in. Terwijl voorheen alleen terugkoelen mogelijk was. De vriestunnel maakt aardappelschijfjes en -blokjes, dunne en dikke frieten klaar om goudbruin gebakken te worden bij de consument thuis.
De bouw van deze vriesinstallatie ging gepaard met een aantal beslismomenten. Johan Verheij, projectleider bij Aviko, somt op: “De installatie moest voldoende capaciteit hebben om de enorme productie aan aardappelproducten van 90°C terug te koelen naar -12°C. Daarnaast waren nog veel vragen onbeantwoord. Nemen we een deels nieuwe installatie op de plek van de oude installatie? Of bouwen we een compleet nieuwe installatie op een andere plek en gaan we componenten hergebruiken?”
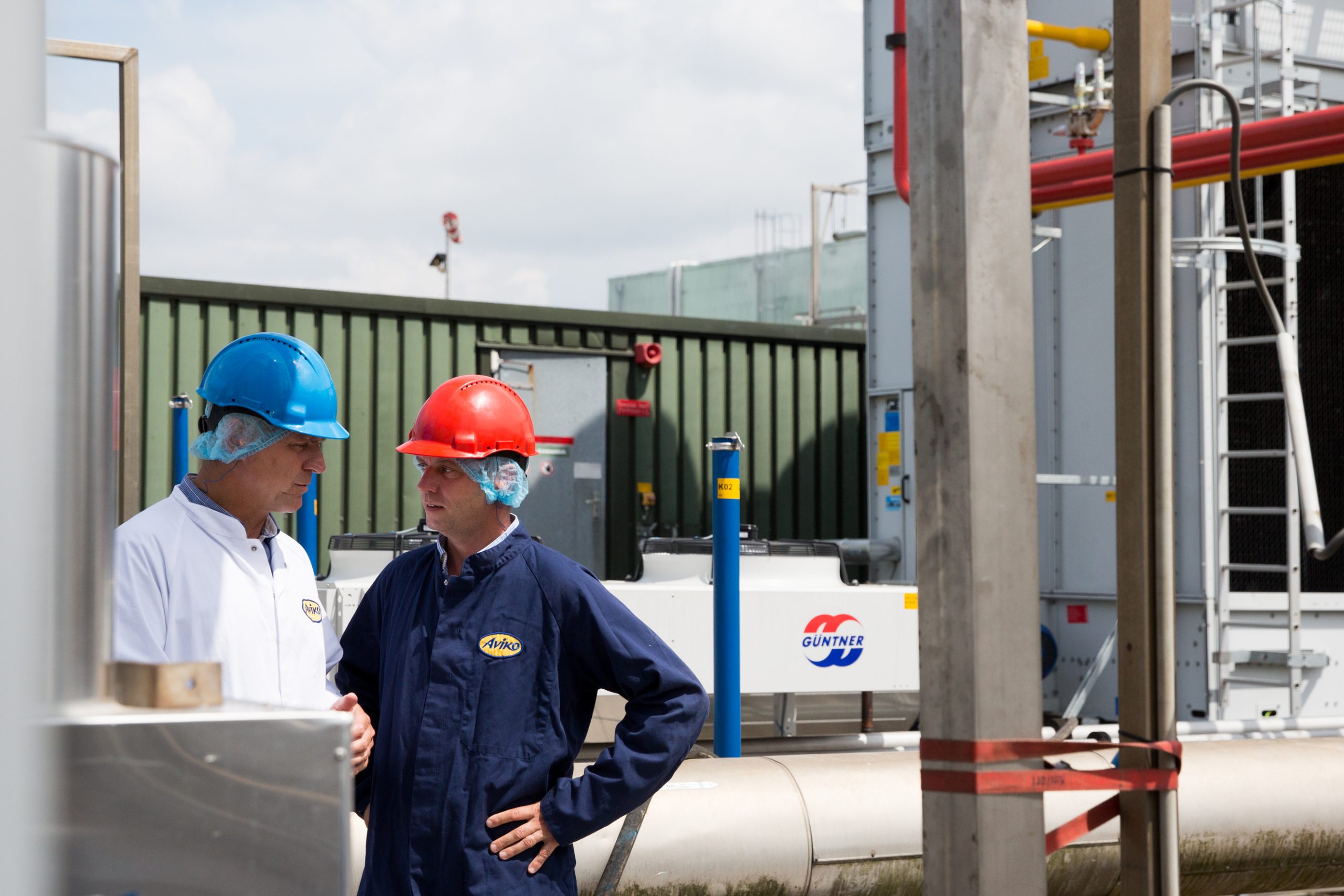
Een ander aandachtspunt was de ombouwtijd. Die moest zo kort mogelijk zijn, want nul productie betekent omzetverlies. Eric van Hees, projectleider bij Equans. “Om tijd te winnen bouwden we in overleg met Aviko een nieuwe prefab-koelinstallatie op een nieuwe locatie. De realisatie nam drie weken in beslag, ongekend snel.”
De twee invrieslijnen in de nieuwe tunnel van Aviko Lomm vriezen de friet met ammoniak als koudemiddel nu stapsgewijs in naar -12°C. Doordat ze afzonderlijk functioneren kan Aviko beter sturen op het productieproces. Dat was voorheen wel anders. Werd de koelinstallatie van de ene lijn uitgeschakeld, dan werd de koeling van de andere lijn ook verstoord. En lag de frietproductie tijdelijk plat. De ontkoppeling van de lijnen resulteert in een onafgebroken productieproces, ook als de koeling van de ene lijn uitstaat.
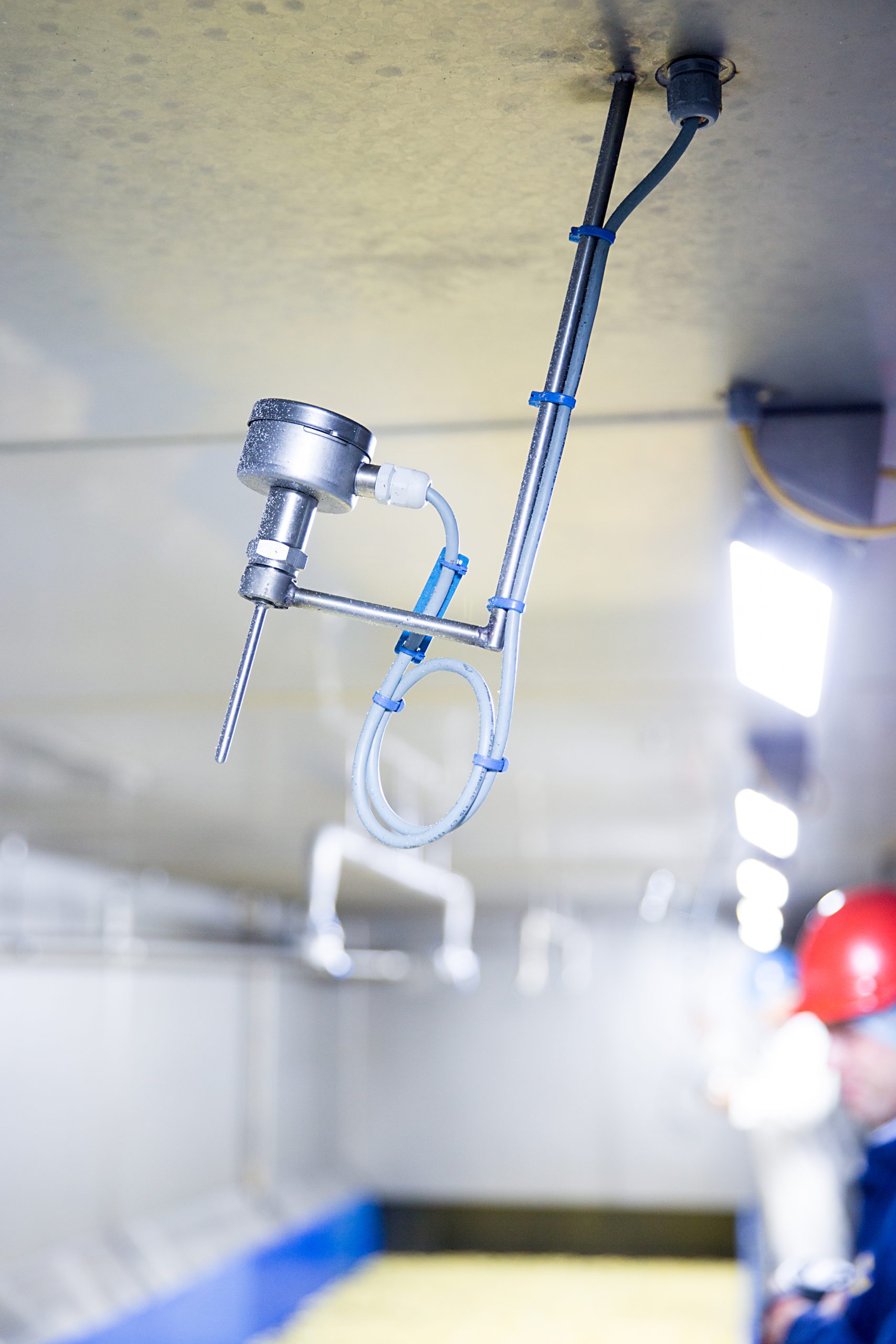
Terwijl Equans werkte aan het ontwerp van de 10-tonstunnel, kwamen nieuwe ideeën tot leven. Van Hees: “Het productieproces zou drie weken stilliggen. Dat zette ons aan het denken. Kunnen we in die tijd andere koelprocessen en -ruimten optimaliseren? Of bestaande installaties demonteren en integreren in nieuwe installaties en ruimten? Tijdens de detailengineering zijn we hierover in gesprek gegaan met Aviko.”
De brainstorm leidde tot meerdere projecten. Van het vervangen of aanpassen van koelinstallaties in de tussenruimte en weegruimte tot het hergebruik van een ammoniakcondensor en het installeren van een nieuwe koeling voor de schakelruimte. Door daar niet met buitenlucht te koelen, voorkomt Equans dat de verontreinigde buitenlucht binnenkomt en de elektronica in de schakelruimte vervuilt. De nieuwe koelinstallatie voor de vriescel zorgt ervoor dat de uitfasering van het koudemiddel freon R22 voor Aviko ook meteen achter de rug is. Verheij: “Equans dacht mee en bleef meedenken, bij elke stap in het project. Daardoor konden we goede keuzes maken, keuzes waarmee we nog jaren vooruit kunnen.”
Communiceren cruciaal
Meerdere opdrachten of niet; de planning bleef ongewijzigd. Aviko moest na drie weken weer op volle toeren kunnen draaien. Dat betekende grote drukte op de bouwvloer, met soms wel 200 man van 12 firma’s tegelijkertijd. Verheij: “In zo’n situatie is goede communicatie cruciaal. Het wel of niet slagen valt samen met goede mensen op de werkvloer. Projectleiders van zowel Aviko als Equans waren beslissingsbevoegd en dag en nacht bereikbaar om uitdagingen of wijzigingen door te spreken. Met dagelijkse overleggen met alle voormannen en wekelijkse bouwbesprekingen met Equans werden risico’s uitgesloten en werd alles in goede banen geleid. Zonder incidenten of andere tegenvallers.”
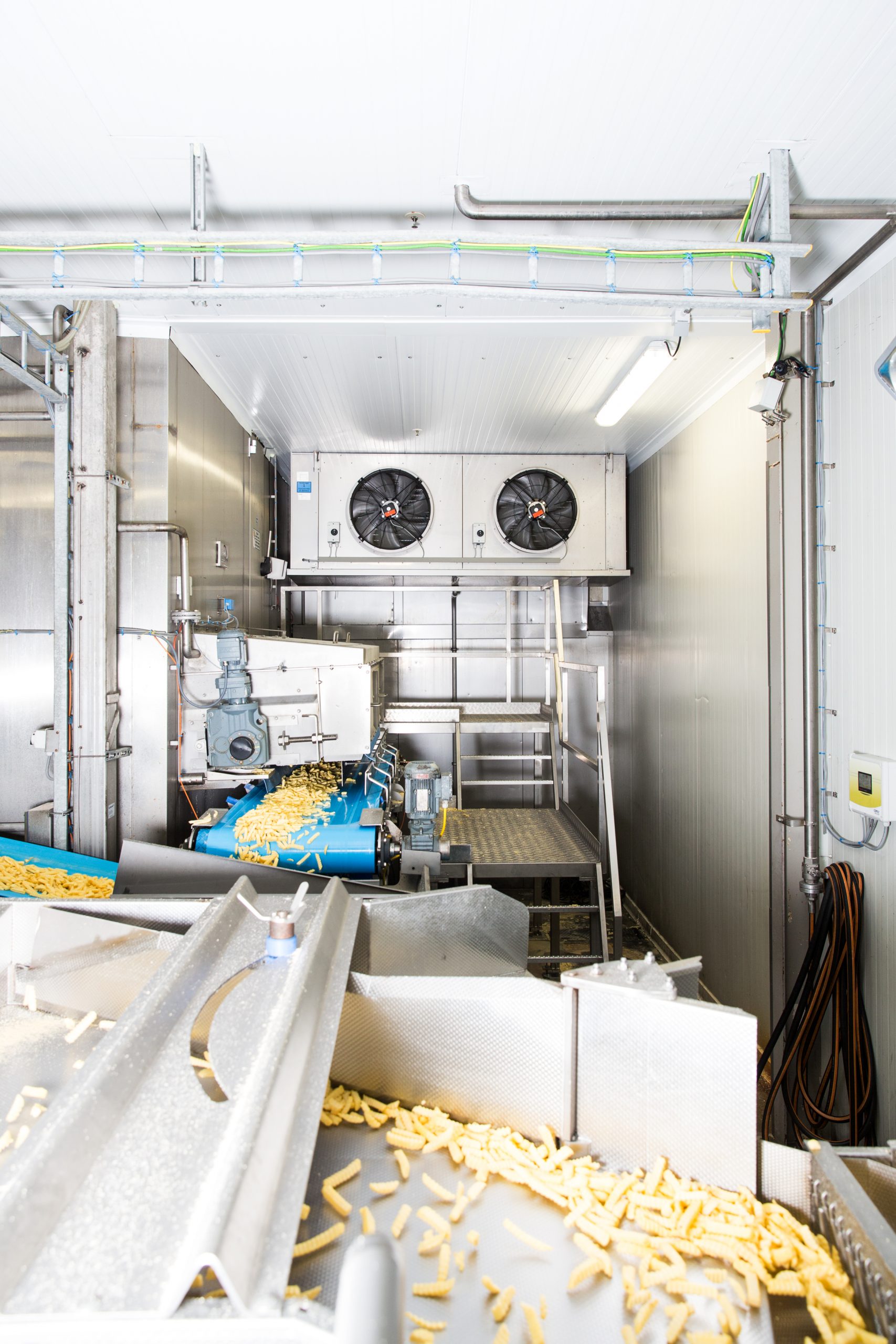
Verheij vervolgt: “Ik ben dan ook zeer te spreken over de inzet van Equans, van ontwerp tot en met realisatie. En het resultaat mag er zijn. Energiezuinige motoren en frequentieregelaars beperken ons energieverbruik. Ook komen we in aanmerking voor de Energie-investeringsaftrek en een innovatiesubsidie. De nieuwe machines leiden tot minder uitval en onderhoudskosten.”
“Dag in dag uit kunnen we vertrouwen op de vriesinstallatie. En we hebben voldoende capaciteit om dagelijks met 2 vrieslijnen 20 ton friet per uur terug te koelen. Deze topprestatie en de goede relatie leidden ertoe dat we Equans hebben gevraagd voor diverse andere projecten op onze hoofdvestiging in Steenderen.”