Phasing out synthetic refrigerants
Is refrigeration part of your business process and does your refrigeration system run on synthetic refrigerants? Then you will be affected by the F-gas legislation of the European Union. These regulations require the reduction of F-gases, also known as hydrofluorocarbons (HFCs) or synthetic refrigerants. In the Netherlands only, around one million industrial refrigeration systems use these refrigerants. These range from agricultural companies to those in the food processing industry.
Impact of the F-Gas Regulation
The purpose of the F-Gas Regulation is to protect the environment by reducing the production and use of F-Gases. These are synthetic refrigerants with a high global warming potential (GWP). The higher their GWP, the greater their contribution to global warming. The regulation consists of a ban on use, a ban on production and a ban on new installations. Read below to find out how this affects your business.
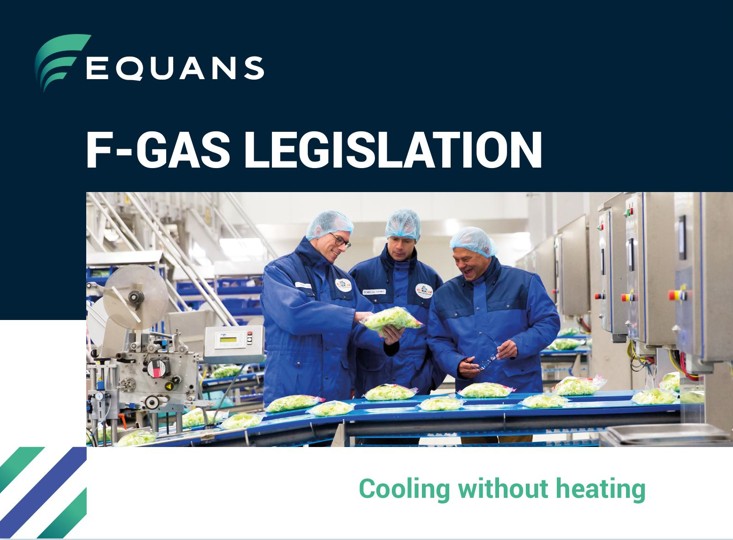
Want to secure your business operations? Take advantage of the opportunities of phasing out synthetic refrigerants.
Request the free information brochureBan on use
The use ban means that you can no longer fill a refrigeration system with an HFC that has a GWP greater than 2,500. This includes the commonly used refrigerants R404A and R507. Until 1 January 2030, refilling is only allowed with recycled and/or regenerated refrigerants. From 1 January 2030, refilling a system with an HFC with a GWP higher than 2,500 will be completely prohibited. The refrigerant R22 is already banned.
Production limitation
Production of F-gases will be phased out from 100% in 2015 to 21% in 2030. This applies, for example, to commonly used synthetic refrigerants such as R134a, R407C and R410A. As a result of this production restriction, high GWP refrigerants will become significantly more expensive and scarce. Take action now to ensure your business does not grind to a halt if a refrigerant suddenly becomes unavailable.
Ban on new construction
From 1 January 2020, no new refrigeration equipment that uses an HFC with a GWP greater than 2,500 may be build. This includes the refrigerants R22, R404A and R507. From 1 January 2022, there is a ban on the construction of new commercial refrigeration equipment that is filled with an HFC with a GWP greater than 150 in the retail and hospitality sectors.
See the overview of restrictions by refrigerant:
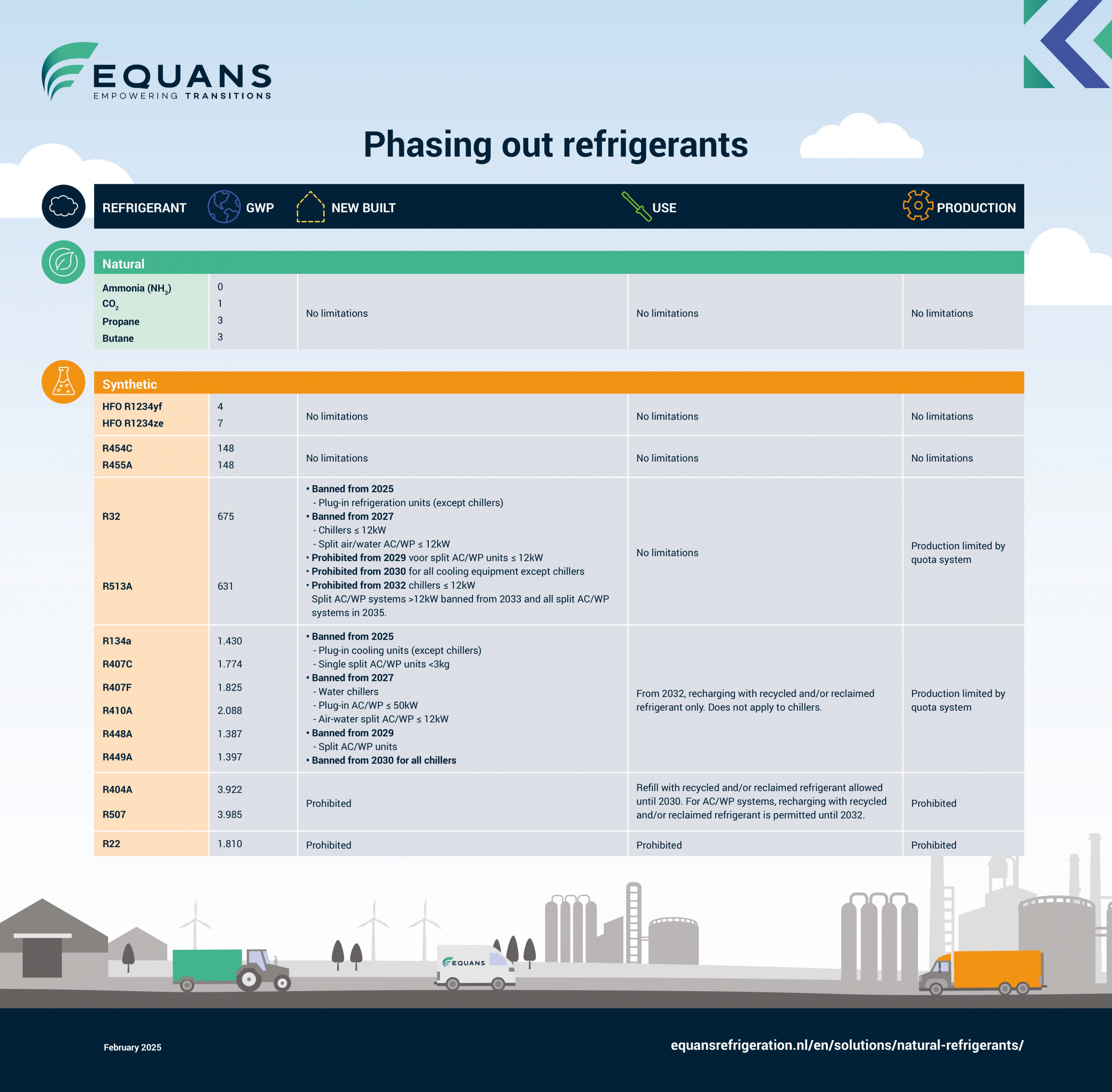
Synthetic refrigerant availability and increased cost problem
Restrictions on the production of synthetic refrigerants caused prices to soar in 2017, making it much more expensive to refill systems with it. In 2020, the prices of R404A and R507 regenerated refrigerants rose further due to a ban on new production of refrigerants with a GWP above 2,500. This was followed by a review of the F-Gas legislation in 2024, including an accelerated phase-out of the refrigerant quota. As a result, the availability and cost of synthetic refrigerants are becoming an issue.
Options for phasing out synthetic refrigerants
Although a well-maintained cooling system can last a long time, you will eventually need to replace it. Especially if it starts to leak. There are several options to help your business comply with new laws and regulations:
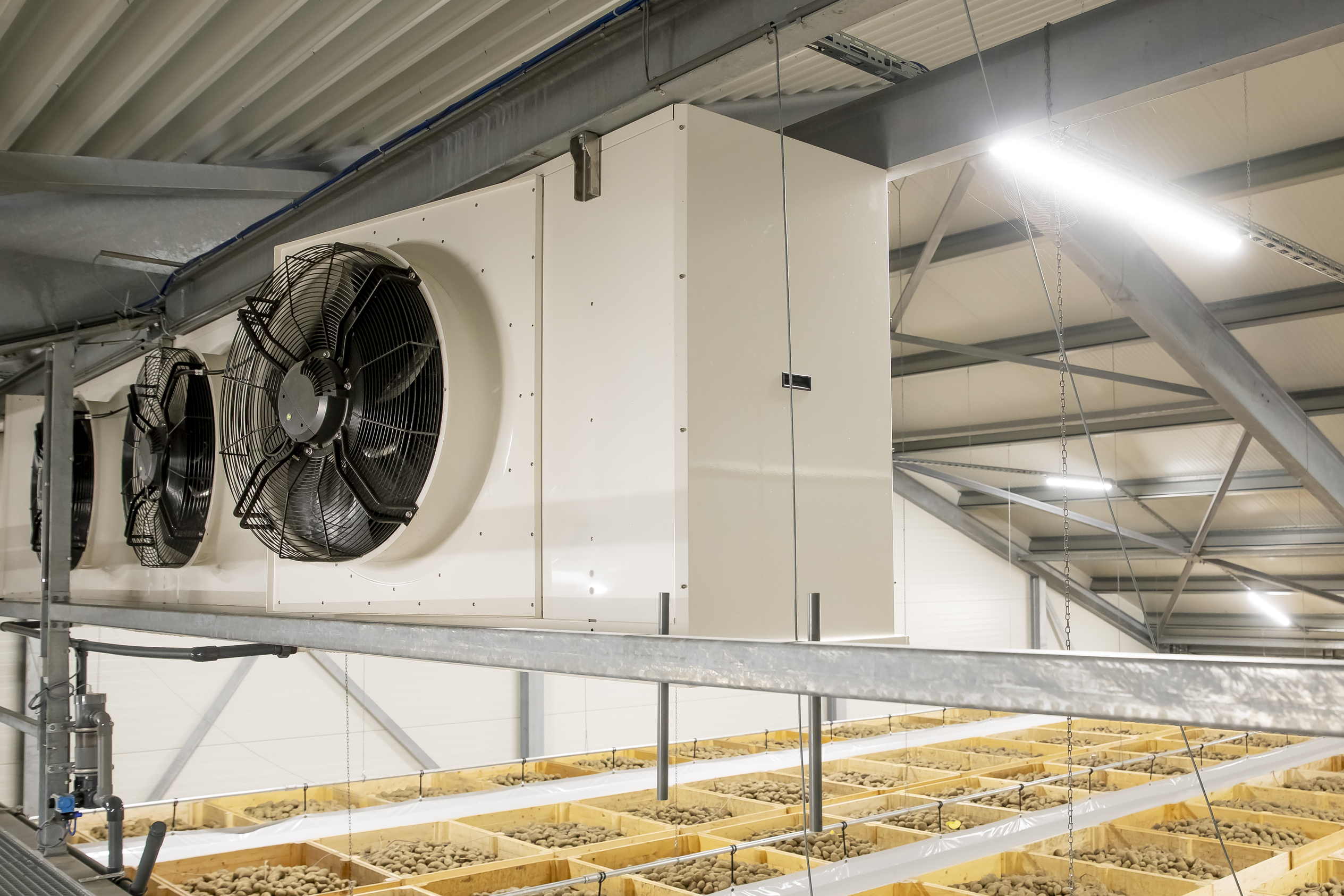
We build a new refrigeration installation using natural refrigerants such as CO2, ammonia, propane or butane. We can also replace an existing installation with one of these. This is the most environmentally friendly, energy efficient and legally compliant solution.
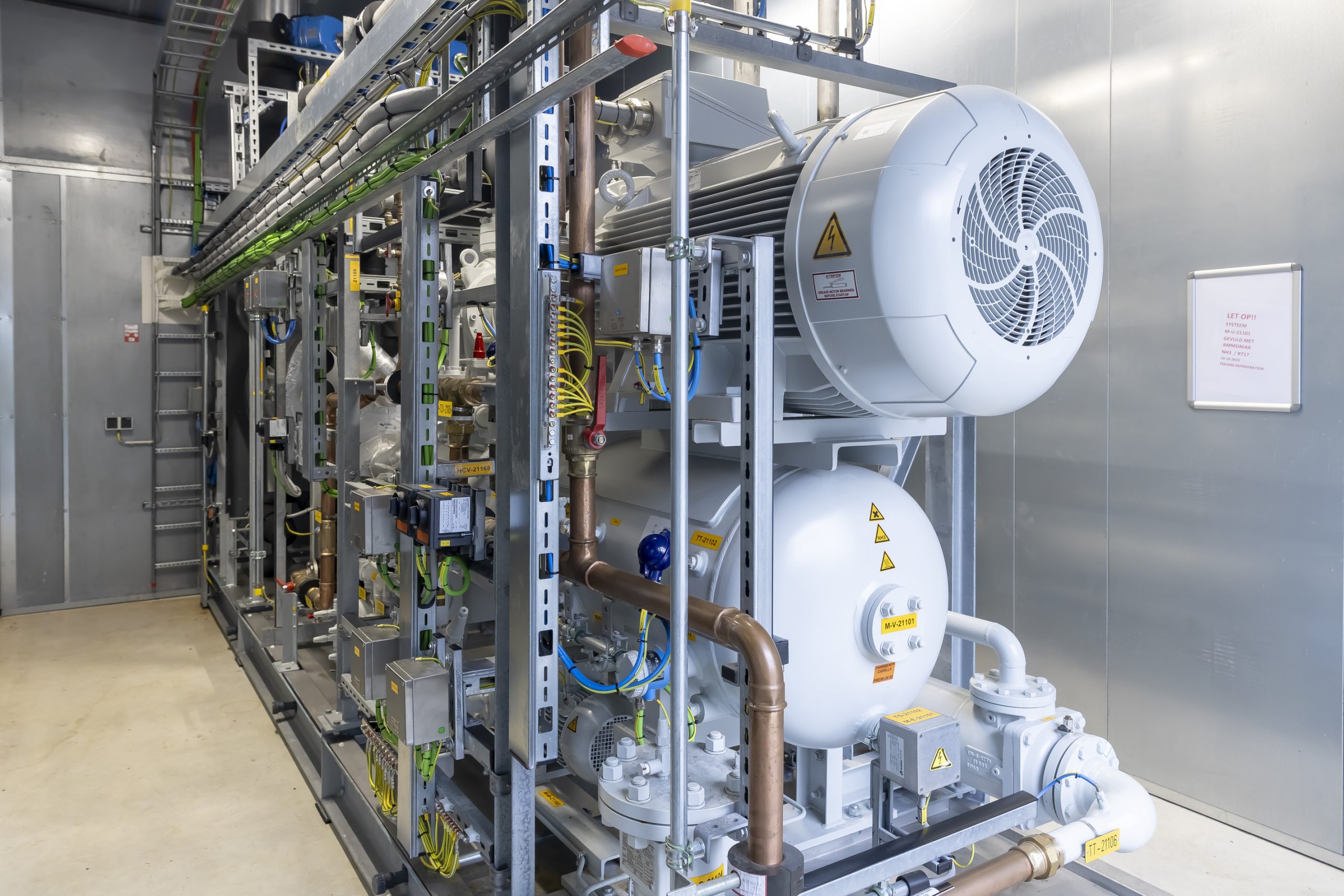
We make an existing installation suitable for another refrigerant by replacing a number of components. A suitable scenario for large, well-maintained refrigeration systems.
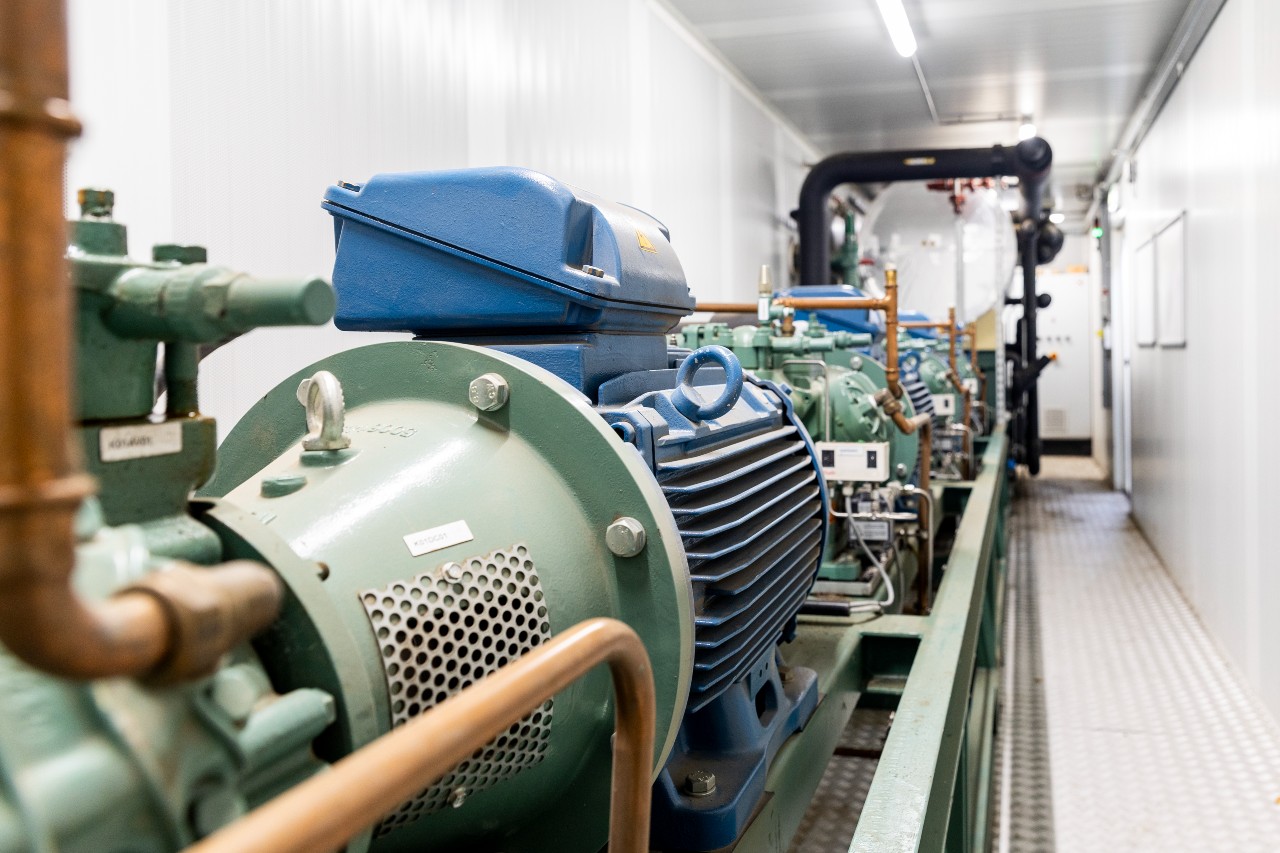
Is your installation under 10 years of age and already prepared for the use of a synthetic refrigerant? We can place a drop-in in a DX-system for R404A and R507. When we do this, the refrigerant is discharged and replaced by an alternative refrigerant. Keep in mind that a drop-in reduces cooling capacity, increases energy consumption and shortens the lifetime of the installation. A drop-in is not possible for pump circulation systems. Moreover, this option is less suitable if the business process is dependent on the cooling system.
How do natural refrigerants contribute to better operating results?
Natural refrigerants such as CO2, ammonia, propane and butane are energy efficient. This results in 25-40% lower energy costs.
You can claim the Energy Investment Allowance (EIA) for natural refrigerant cooling and freezing technology. This allows you to deduct 45% (2019) of the investment costs from your taxable profit, in addition to the usual depreciation. On average, the EIA gives you a 10% tax benefit.
Cooling with natural refrigerants helps to reduce quality losses in the cooled product, especially in the food industry. You can therefore benefit from higher yields and lower (processing) costs.
Cooling with natural refrigerants fits in with a sustainable production chain. Approximately 3% of the total electricity consumption in the Netherlands is used for cooling purposes. Natural refrigerants help to reduce this share and make businesses more sustainable.