Drying without gas
Dehumidification of products or rooms is often achieved by heating with direct-fired gas heaters. This not only produces harmful CO2, but also water from the combustion process. Evaporating the water requires additional energy. This is a wasteful process because water can be dried in more efficient ways. Besides energy efficiency, there is another reason to redesign your drying process: the energy transition. This mandatory transition from the use of fossil fuels to using energy from renewable sources forces you to look for alternative drying methods.
Improve energy efficiency
If you need to switch to a more sustainable way of drying, we can assist in finding the most energy efficient solution. Efficient drying technology can include using a heat pump or condensate drying system, with heat recovery as an option. Depending on how we design the drying process, we can generate at least 4 times more heat with the same amount of energy!
Drying with a heat pump or condensation dryer
Heat pump drying utilises air heated with a heat pump. The heating causes the relative humidity to drop and the air can absorb moisture again. The air can then be used to dry a room or a product. Condensation drying is a technique we mainly use when drying at lower temperatures. Here, the air is recirculated and you do not need to use outside air. The recirculated air is also cooled, with the moisture in the air being captured by condensation in the cooler. This technique is very suitable for drying agricultural products such as onions, celeriac and potatoes.
Higher COP with customisation
Of course you can create a more sustainable drying process with a standard heat pump. But did you know that a customised version can make the drying process even more energy efficient? We design the customised heat pump to fit completely into your production process. In doing so, we reuse heat released from other processes and equipment. By designing a customised heat pump and integrating it into your business process, we can avoid the use of unnecessary heat exchangers and the related temperature losses. Customisation therefore guarantees the highest COP.
Temporary solution when the grid is overloaded
Although we only implement heat pumps running on electricity, it is possible to use gas engines on the heat pump. This is a suitable alternative for companies whose electric grid load capacity is limited due to grid congestion. If the restriction is lifted in the future, we can always convert the heat pump drive to electric.
Future-proof drying with natural refrigerants
Our drying technology often uses a natural refrigerant. These refrigerants have good thermal properties and can generate the most heat with 1 part of electrical energy. A drying system using ammonia, for example, is typically up to 40% more economical. Because of its high COP, ammonia can be used with a lower electrical connection with reduced fixed costs.
Payback for energy efficient drying
Although the investment for gas-free drying is higher than for conventional technology, you will recoup most of it through energy savings. If this does not cover the entire investment, you can apply for the SDE++ subsidy. Our sustainable drying technology can also be used in combination with solar panels. With our assistance, your solar energy can power your drying process.
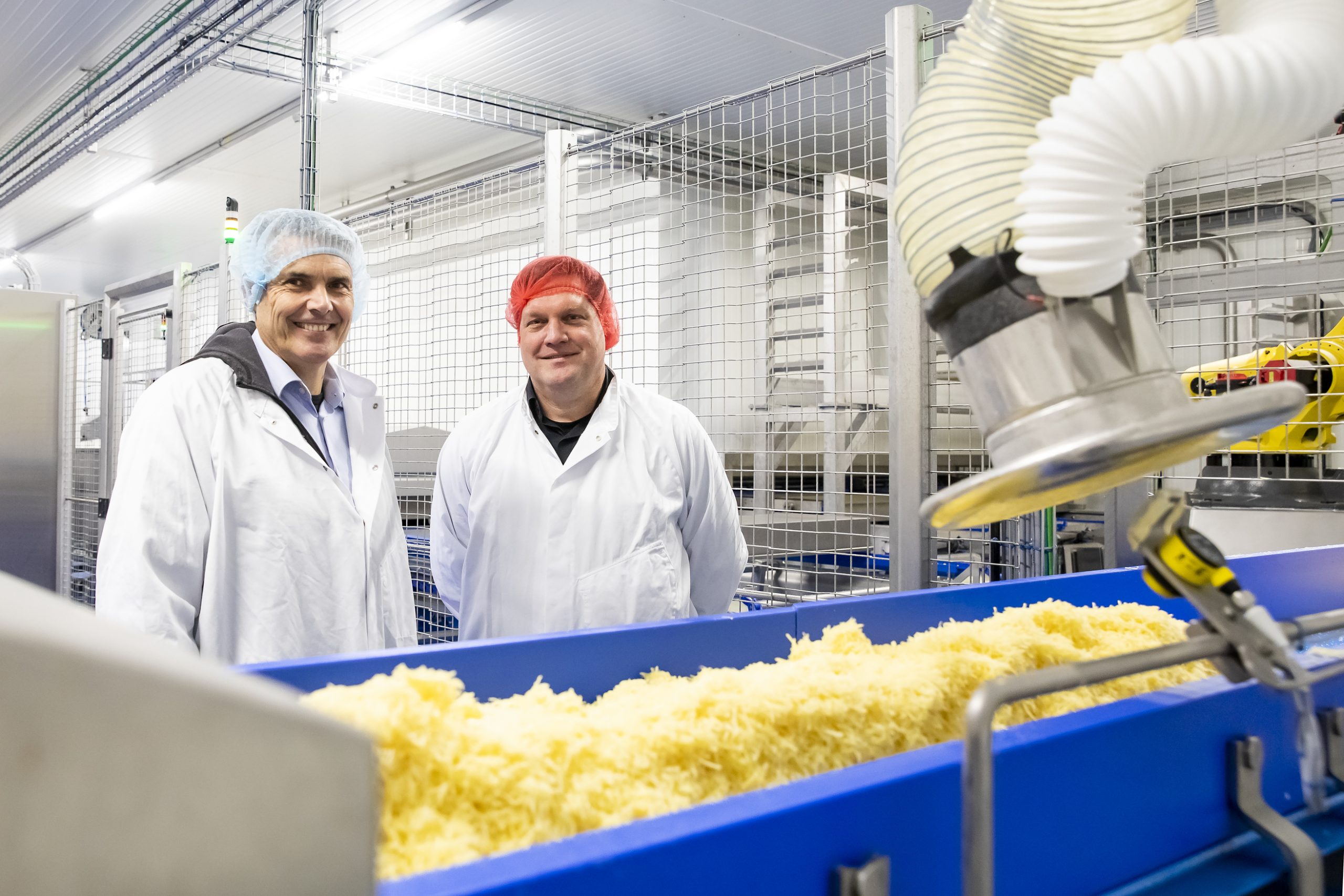
For Grozette’s new production facility we built a drying tunnel with an integrated cooling and heating system. It enables the cheese processor to dry its cheese products without gas, and therefore cost-effectively and sustainably.