The NIVU partnership combines the entrepreneurial spirit of Gerard van Nieuwenhuijzen with the product knowledge of Jack van Vugt. They grow sugar beet, onions, wheat and potatoes on 400 hectares of almost continuous fields. Tractors and machinery are equipped with computers and sensors that automatically record all actions and conditions in the fields and on the farm. Which tractor is doing what, where and when? What is the condition of the crop and soil in each field? This is valuable information that both farmers use to give crops and soil the precise nutrients they need and limit the use of pesticides and fertilisers.
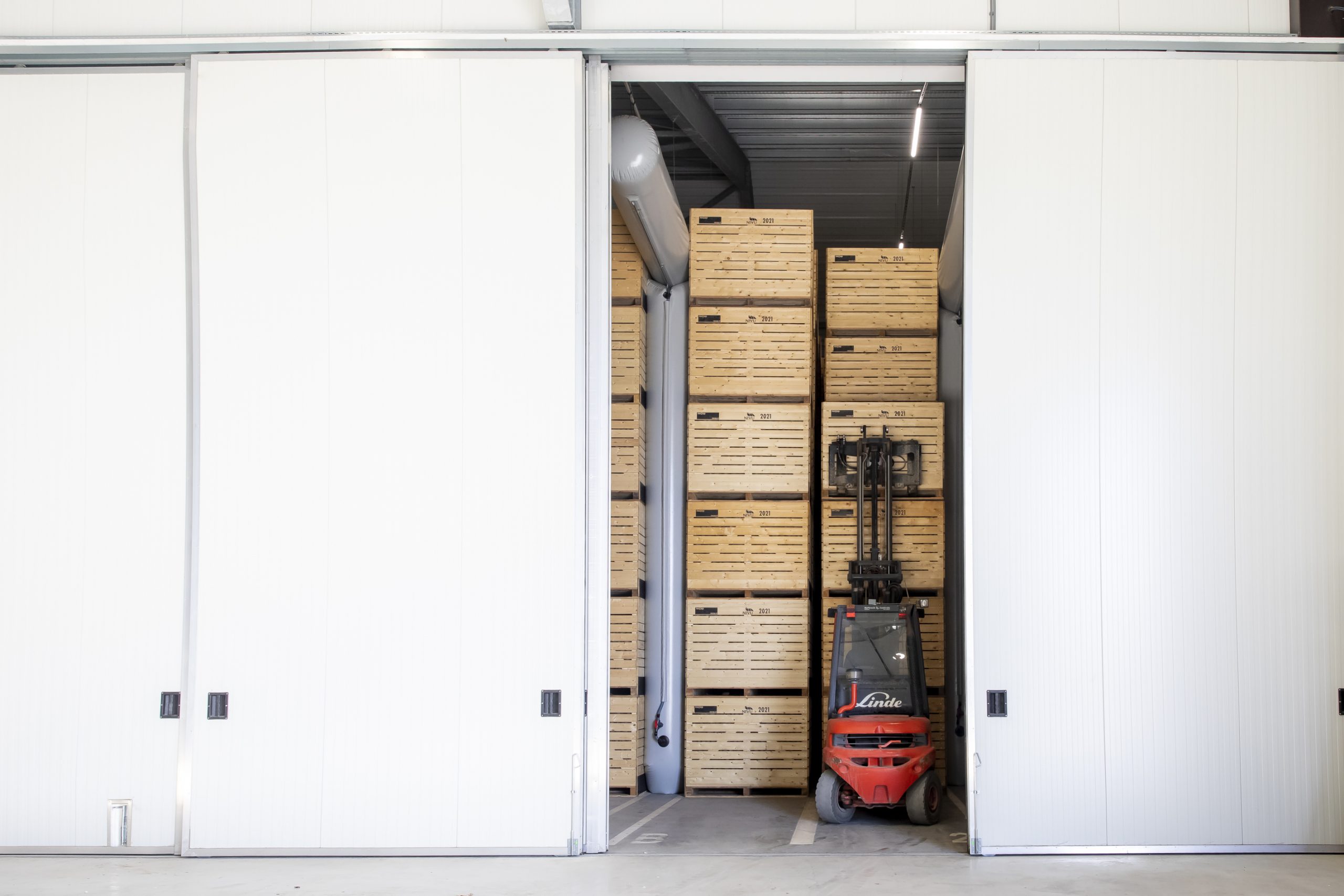
Just because potatoes are in good condition in the field doesn’t mean they stay in good condition in the warehouse. Therefore the gentlemen knocked on the door of Equans for a cooling system. “In our old bulk potato storage, we cooled and dried with outside air. We wanted to switch to box storage to reduce bruising and improve product quality. It also allows us to be more flexible and deliver all year round. You open the door and take a few crates out, while the rest of the cell remains intact,” says Van Vugt.
“We also wanted to expand into new markets. This increased our need for better preservation”, adds Van Nieuwenhuijzen. “Margins in this industry are low. If we want to serve the export market, we need to supply higher quality potatoes. Mechanical cooling is then a prerequisite.”
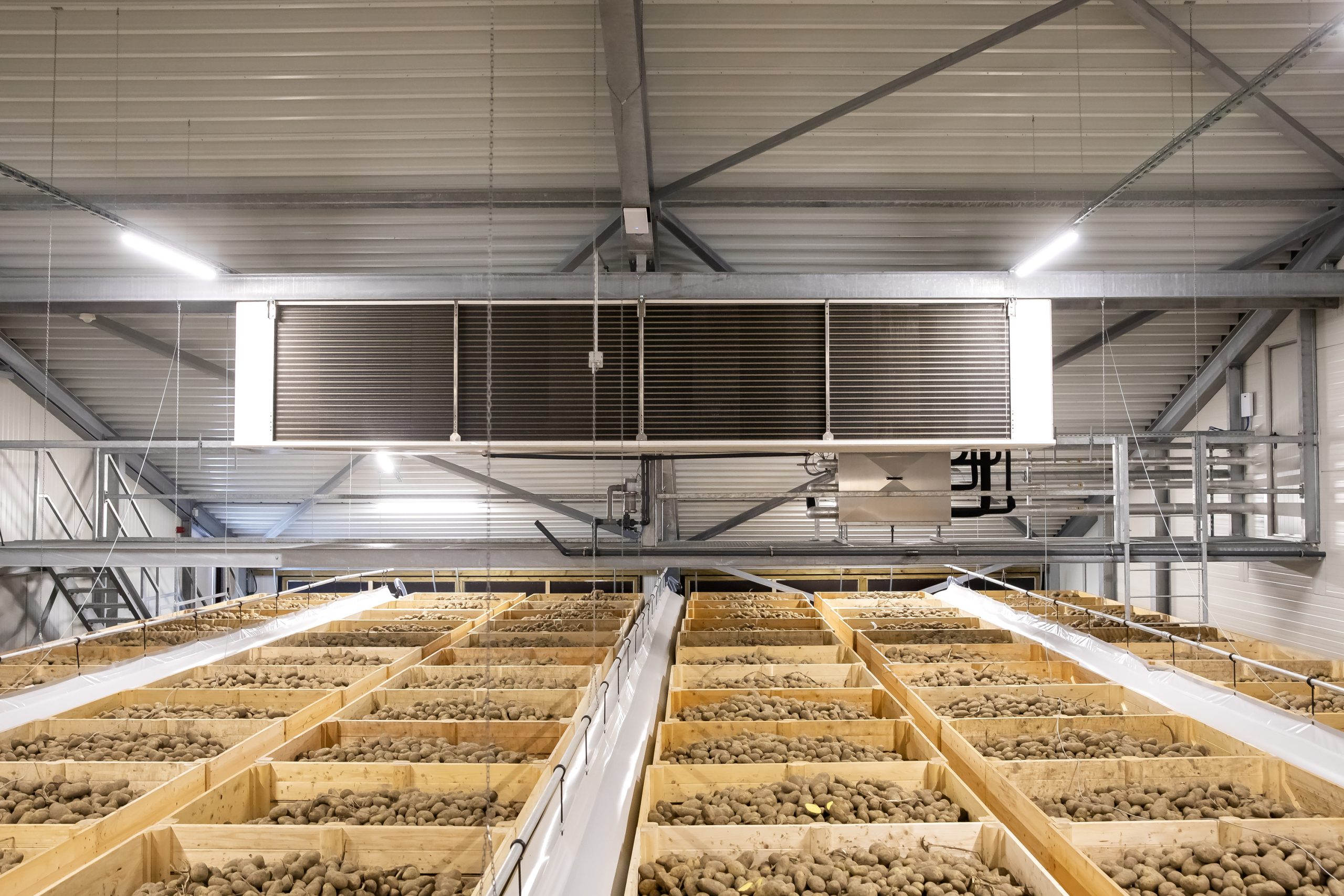
In 2021, an impressive storage shed with a condensation drying system was built on their plot. With a large workshop in the middle and six cold stores on either side, the shed will be able to keep 5,400 crates of potatoes in optimum condition. Van Vught shares his first impressions of the condensation drying installation: “The settings can be adjusted cell by cell, even to a tenth of a degree. Unlike before, we now know exactly what is happening and have control over the product. The Agria is a difficult-to-store potato that rots easily if it gets wet. But the new system is so advanced and has so much ventilation capacity that we can now dry to the maximum. Even in temperatures as low as 5.6°C. After we put the potatoes in, we close the doors and 48 hours later the product is dry.”
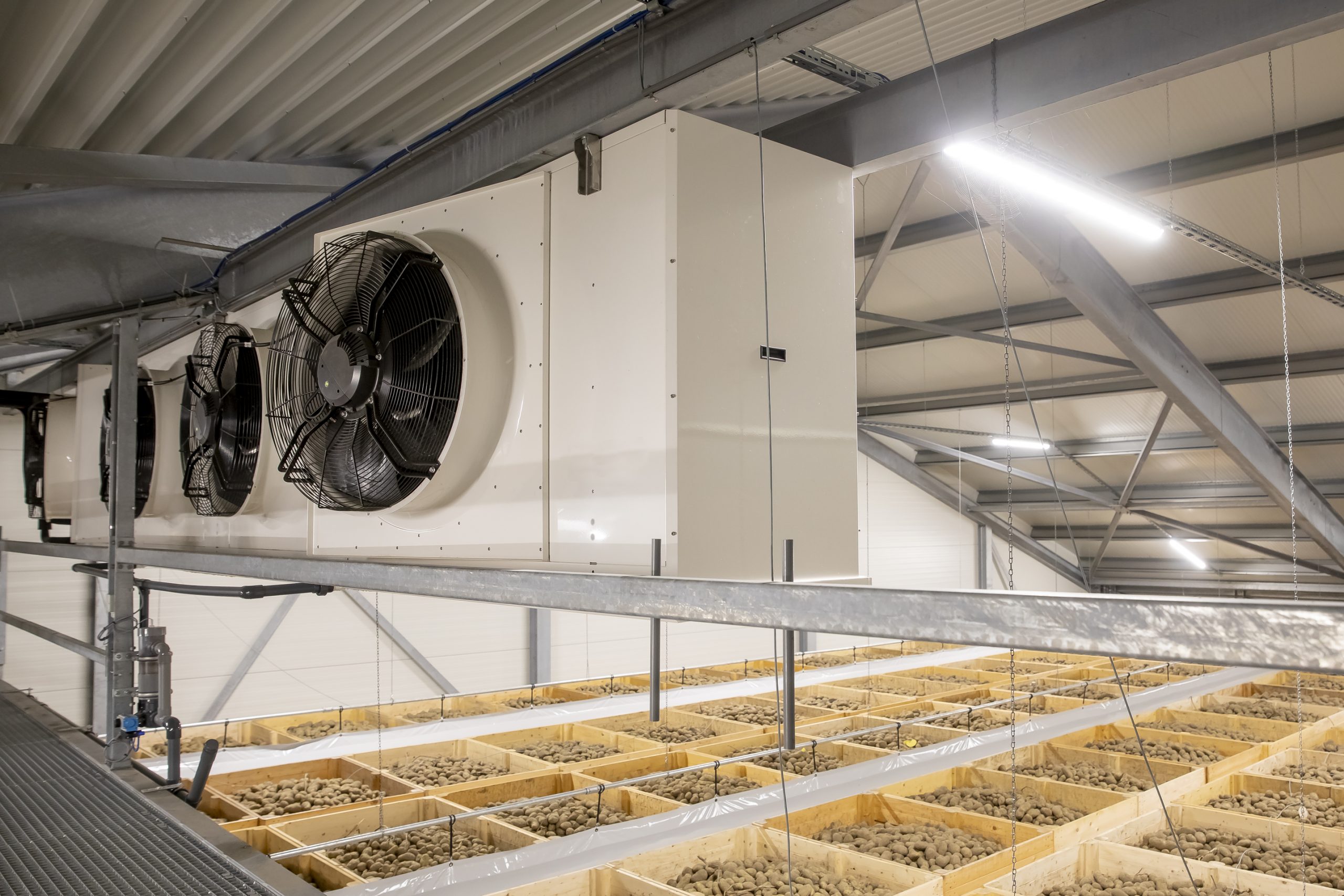
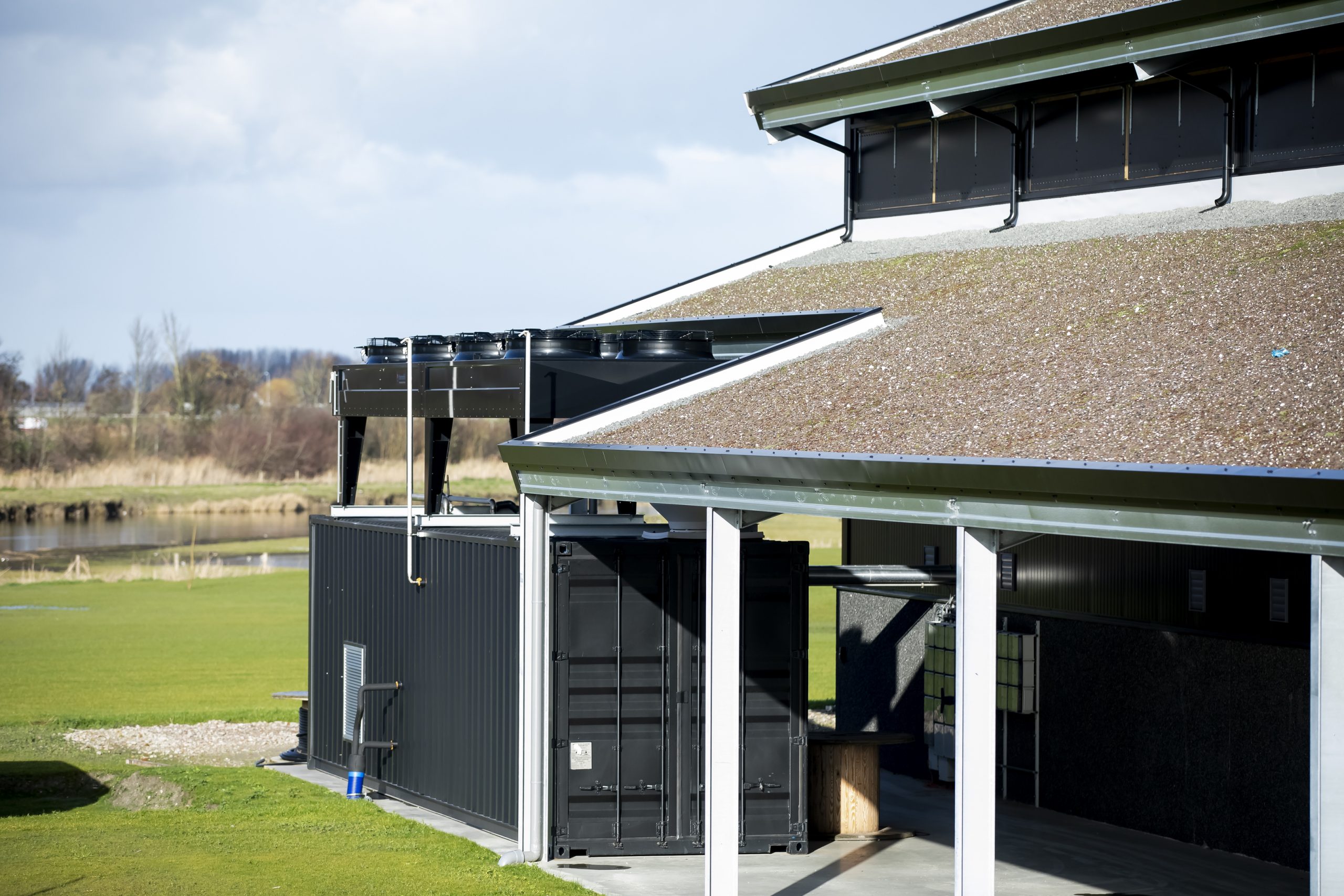
The cooling system uses ammonia, which is more precise than any other refrigerant and results in constant temperatures. “We think we can achieve half the storage losses. So far it looks promising”, says Van Nieuwenhuijzen. The biggest gain, he says, is in moisture retention. “We can see how much the product dehydrates and therefore how much is lost in storage. With the old system we had 10% dehydration, now we hope to end up with 5%. With a few tonnes of potatoes, that is a huge gain. The less dehydration, the better the quality of the potatoes. It keeps the potatoes hard and more vital, with less bruising and peeling waste.”
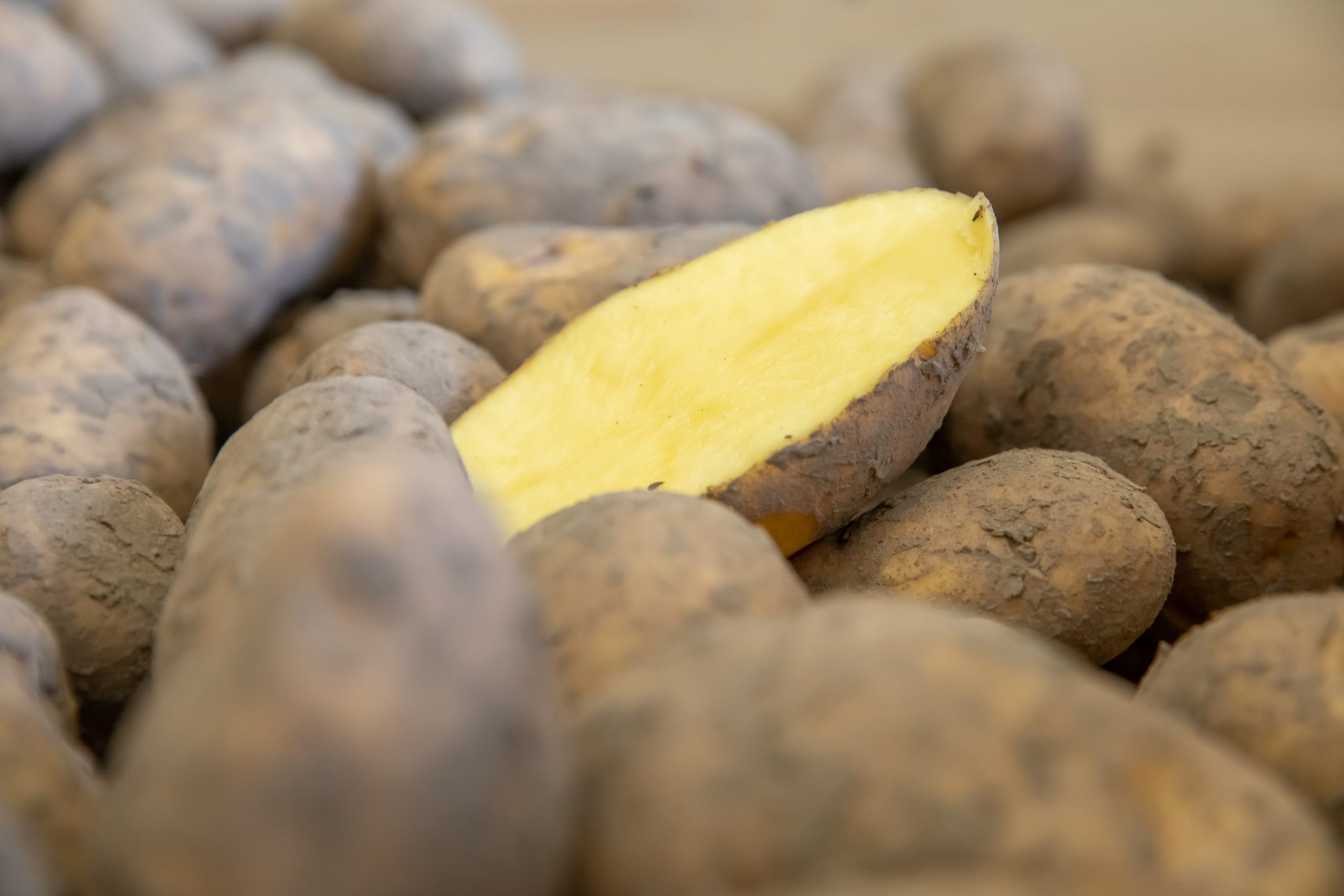
The aim is to store the potatoes until July or even August. “Because we can now store the potatoes so early, they stay more inactive and germinate less. This is positive, also because we want to use as few sprout inhibitors as possible”, says Van Vugt.
“We keep the product at a constant temperature and can regulate and anticipate very precisely when it is necessary. The condensation drying system not only adds value to good potatoes, but also provides better risk management for poorer quality potatoes. With this system, a poor-quality batch is completely isolated and we can prevent further losses. In addition, the well-regulated CO2 extraction ensures that the baking quality of the potatoes is maintained.”
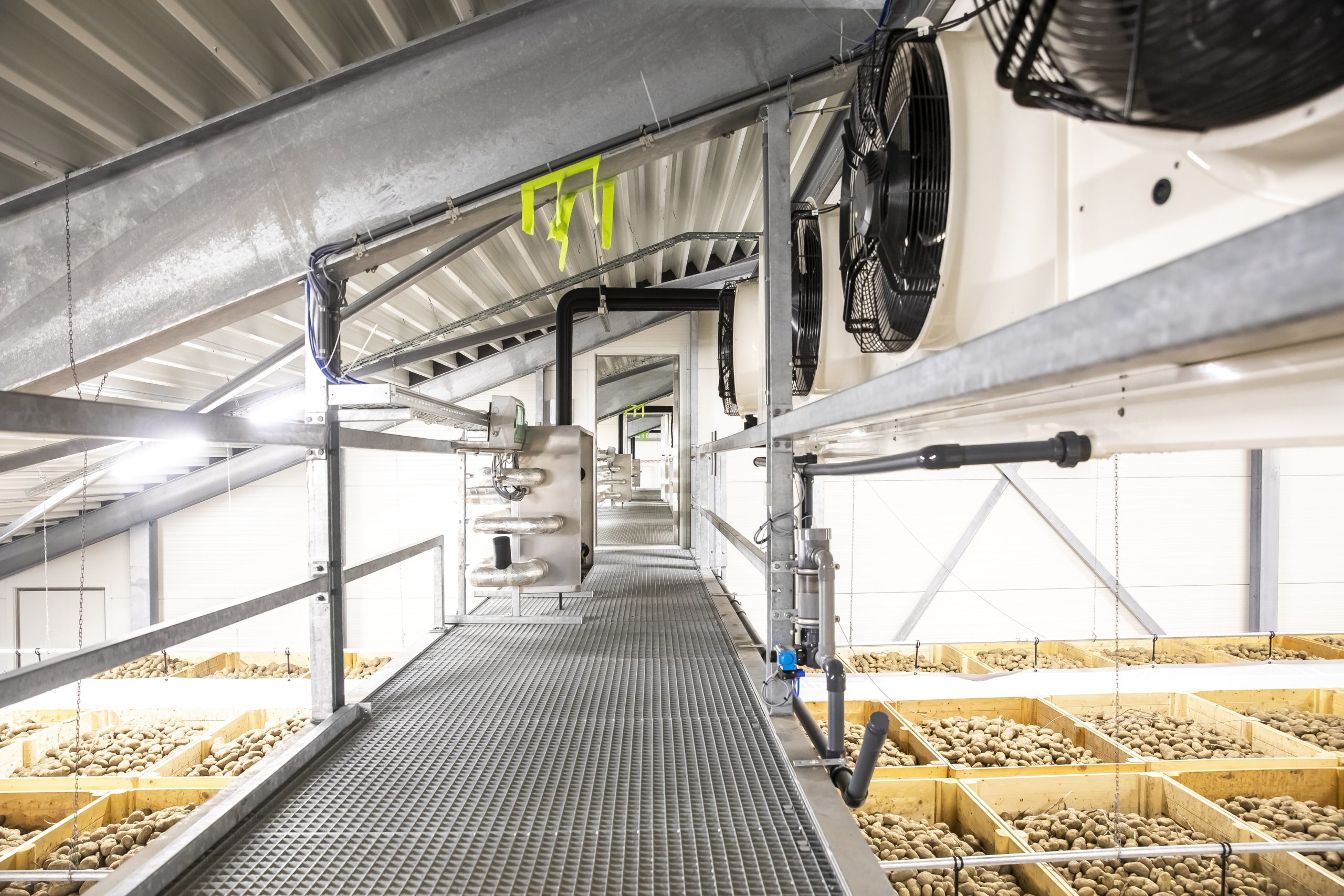
In addition to the condensation drying system, Equans has also implemented other features in the luxurious and spacious warehouse. A walkway over the crates makes product inspection and maintenance of the refrigeration system easier, faster and safer. Although NIVU doesn’t often use the hatches for outside air, they do add flexibility to the storage system. It allows them to dry and store other crops such as onions, carrots and tubers. In addition, by using the heat released during cooling for the condensation drying and heating processes, NIVU can manage energy flows in a more sustainable way.
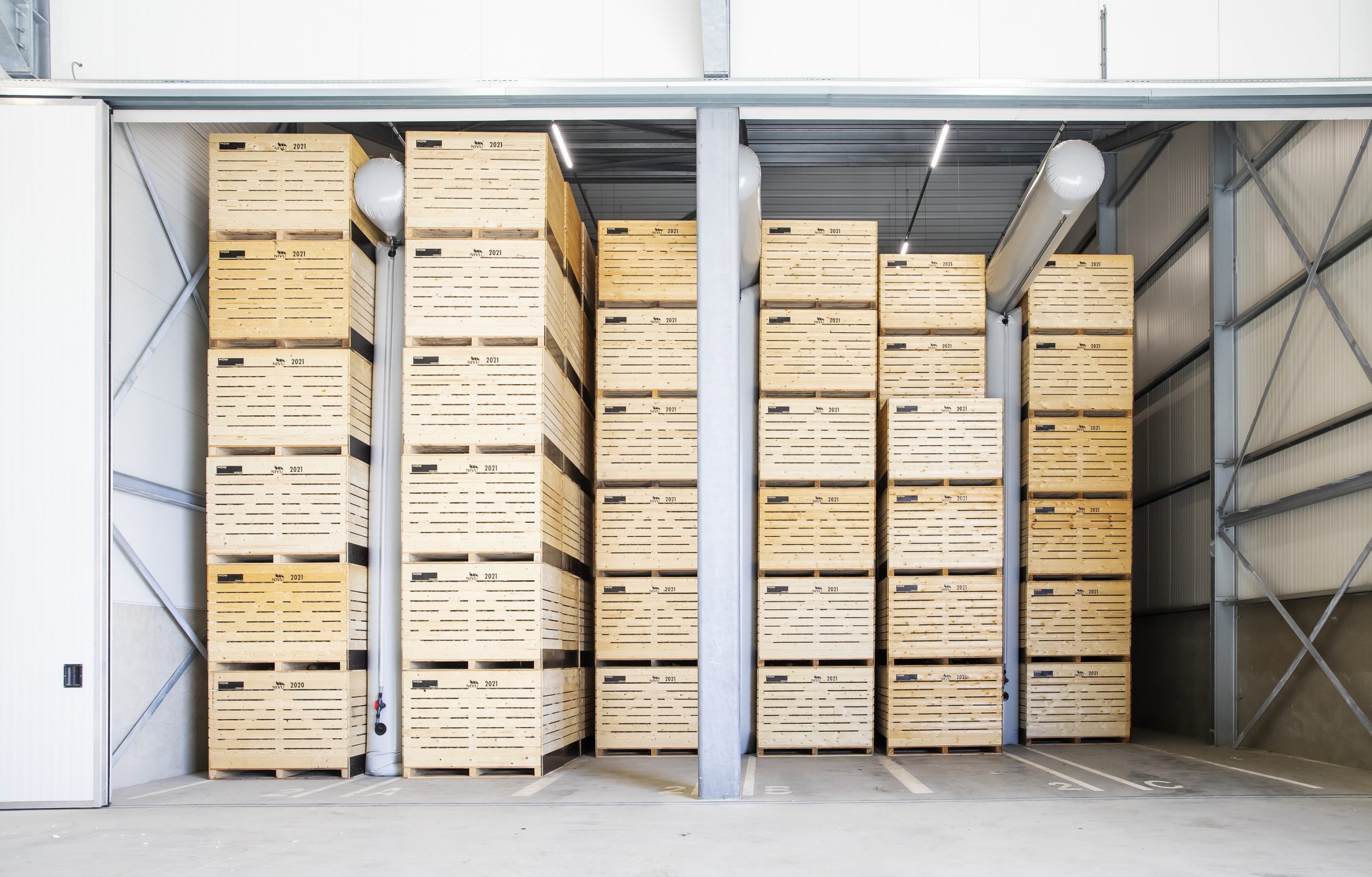
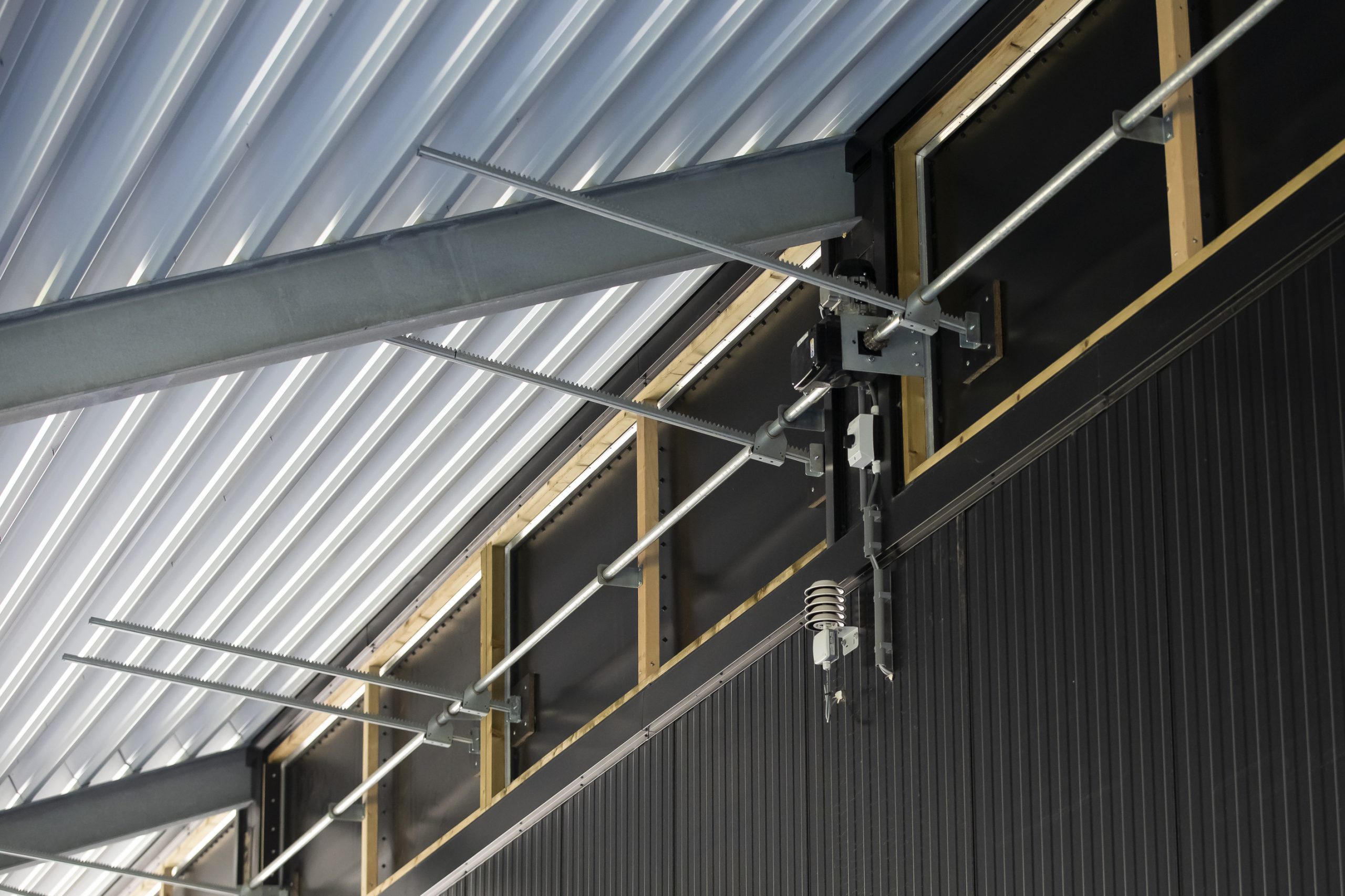
The potatoes can be traced to the last centimetre in the warehouse thanks to an innovative system. NIVU has placed tags in the floor on each crate and at each crate location. These give a signal to the forklift trucks, making their location known. In this way, every forklift driver knows which crate he is carrying. Van Nieuwenhuijzen explains: “Thanks to the automatic crop registration, we know exactly which potato it is and which plot it comes from when we put it in the storage. With the new tracking system with tags, we also know which crate the potato goes into, where it is in the store and when we take it out. No other track-and-trace system can do that yet.”
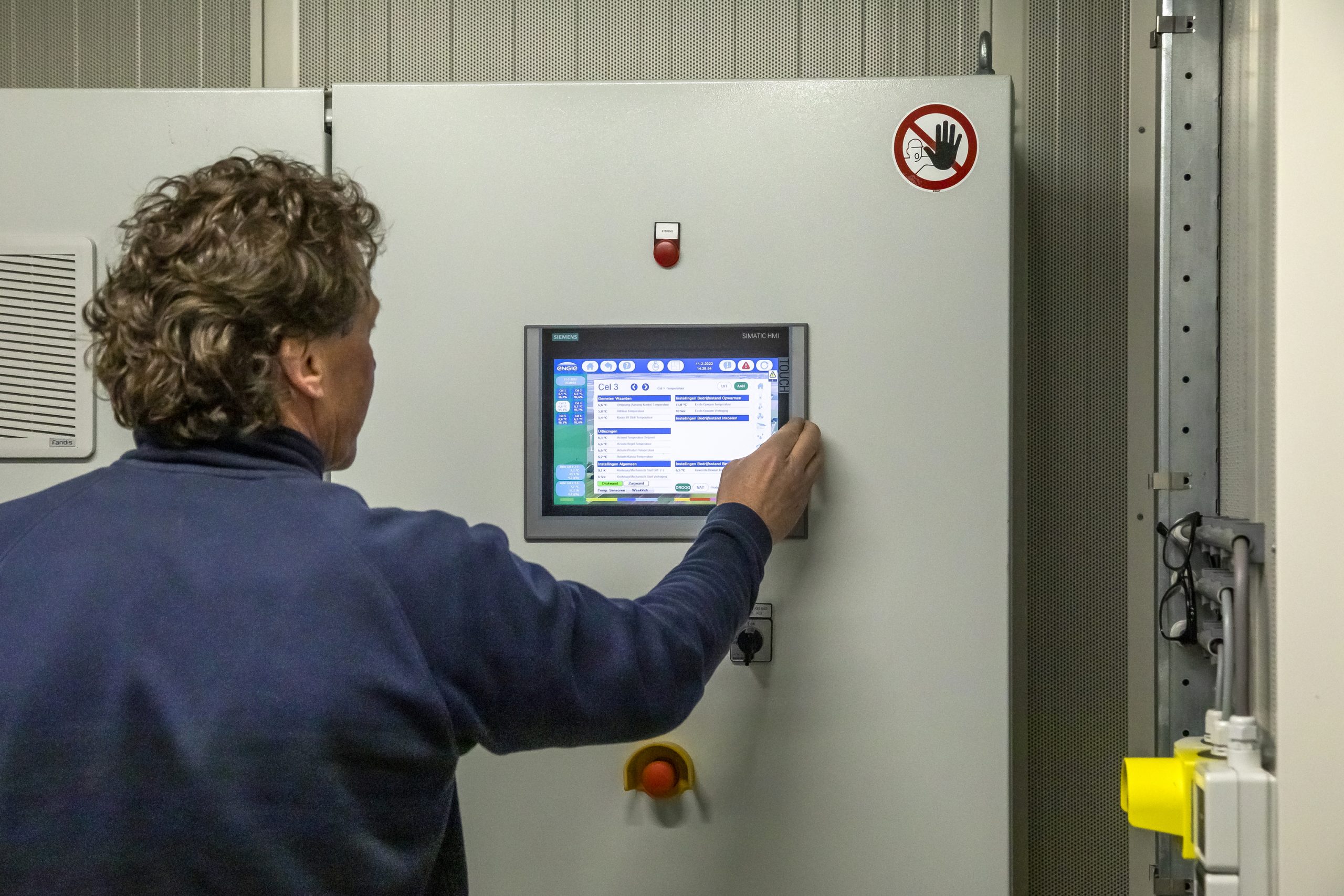
Van Vugt also confirms that the tracking system is worth a lot: “When we see something about the product in the top box of row 3 during the quality checks, then we can immediately check if the other potatoes from that plot show the same symptoms. With this information, we can take immediate action, for example by adjusting the storage conditions. The great thing is that this season’s storage data will provide valuable information for next year. What condition did the produce arrive in? What conditions did we offer? And how did it come out? With this data, we can take quality to the next level each storage season. We are looking forward to it.”
Equans Reference NIVU
"*" indicates required fields
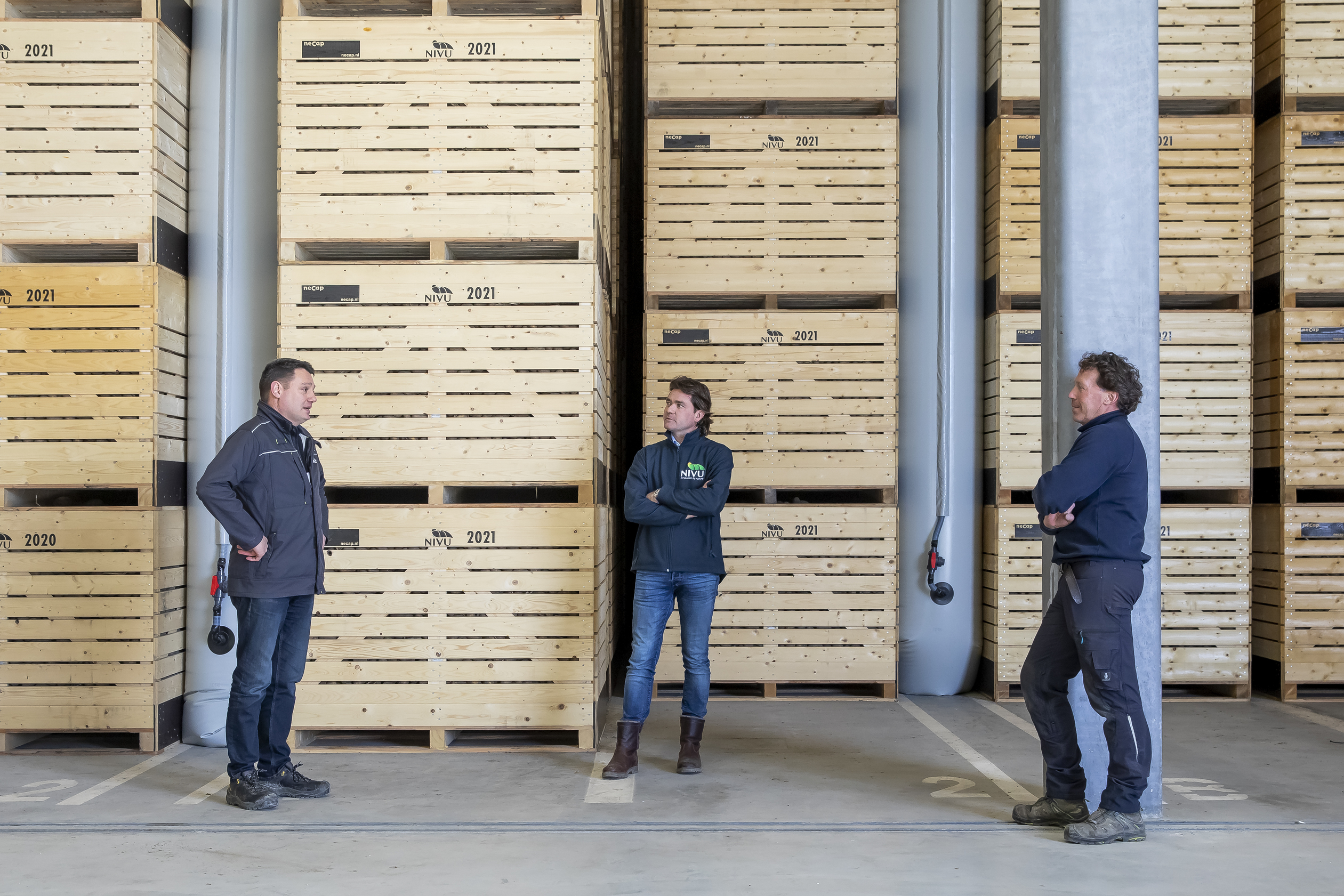