What are the regulations around R22?
According to European legislation (regulation on Ozone Depleting Substances – EC 1005/2009), the R22 refrigerant is not prohibited in your cooling installation. According to the regulation, ‘use’ for new construction and service purposes is prohibited (Article 3). Refilling and replenishing installations with the R22 refrigerant falls under ‘use’ and therefore is prohibited.
This means that existing R22 installations may continue to operate, but no activities with the refrigerant may take place outside the installation. In the event of a leak, your installation is likely to fail for an extended period of time and can jeopardise the continuity of your business process. The refrigerants R401A, R402A, R408, and R409A are mixtures and contain R22 in addition to HFCs. These mixtures, therefore, fall under the same rules as for R22.
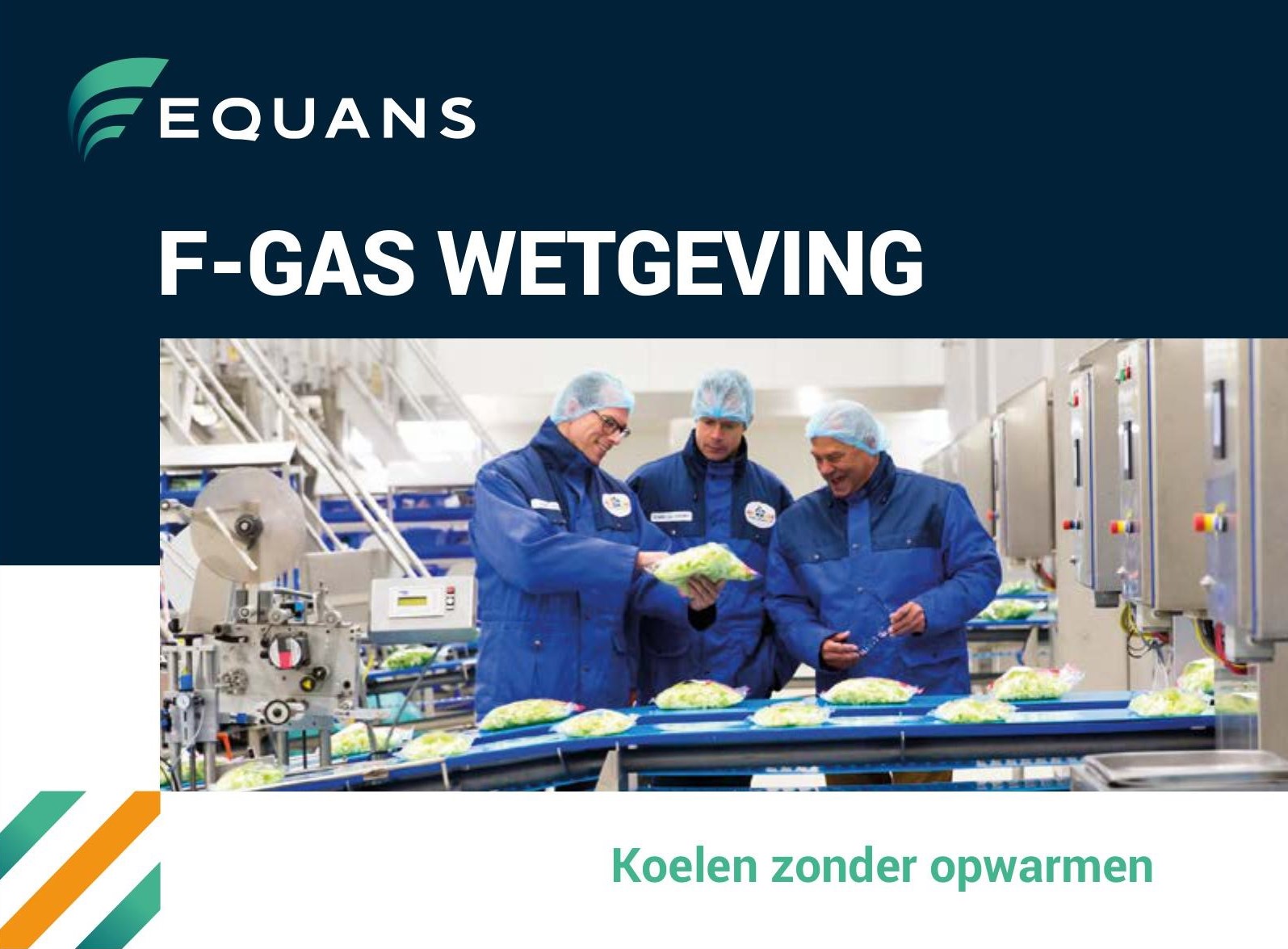
Je bedrijfsvoering veiligstellen? Benut de mogelijkheden om synthetische koudemiddelen uit te faseren.
Request the free information brochureHow can I phase out R22 refrigerant?
If you have a refrigeration system that is cooled with R22 or R12, you can choose to continue using it, or you can choose a drop-in, a conversion or a new build. To make the right choice, it is important to consider a number of factors like the age, number, condition and cooling capacity of your installations.
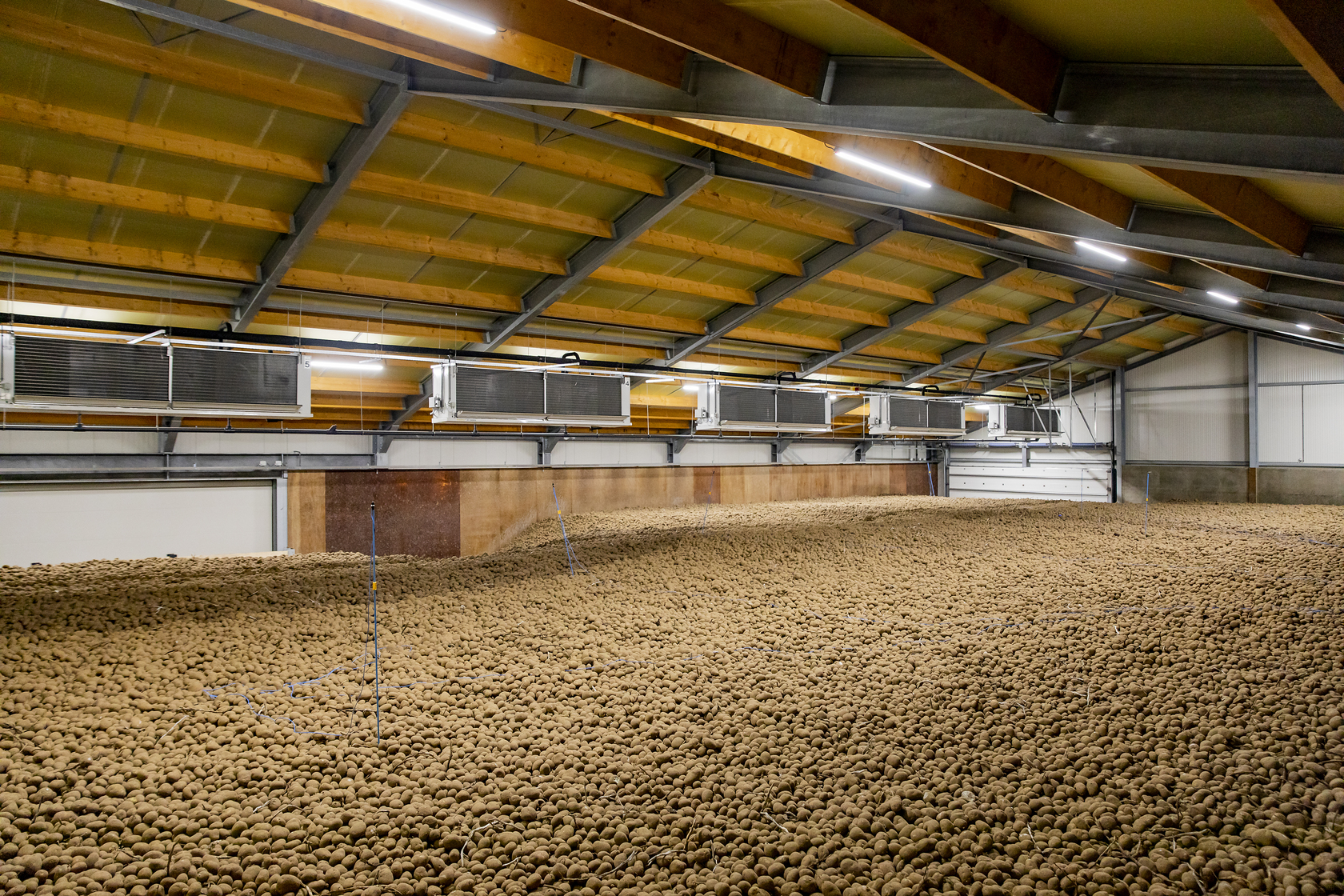
Reliable and well maintained installations without leaks can continue to operate. You may continue to repair your R22 refrigeration system and replace components under the condition that the R22 refrigerant remains in the system. Legal inspections are also still required for R22 systems.
What is not allowed is the temporary draining of the refrigerant. Repairs that require R22 to be drained are no longer allowed. Refilling with R22 is also prohibited.
Is refrigeration critical to your business process? Then running the system is less suitable. After all, in the event of a leak, the system is at risk of long-term failure, because as of 1 January 2015, it is illegal to refill refrigeration systems with R22. If you choose this scenario, have your refrigeration system checked regularly.
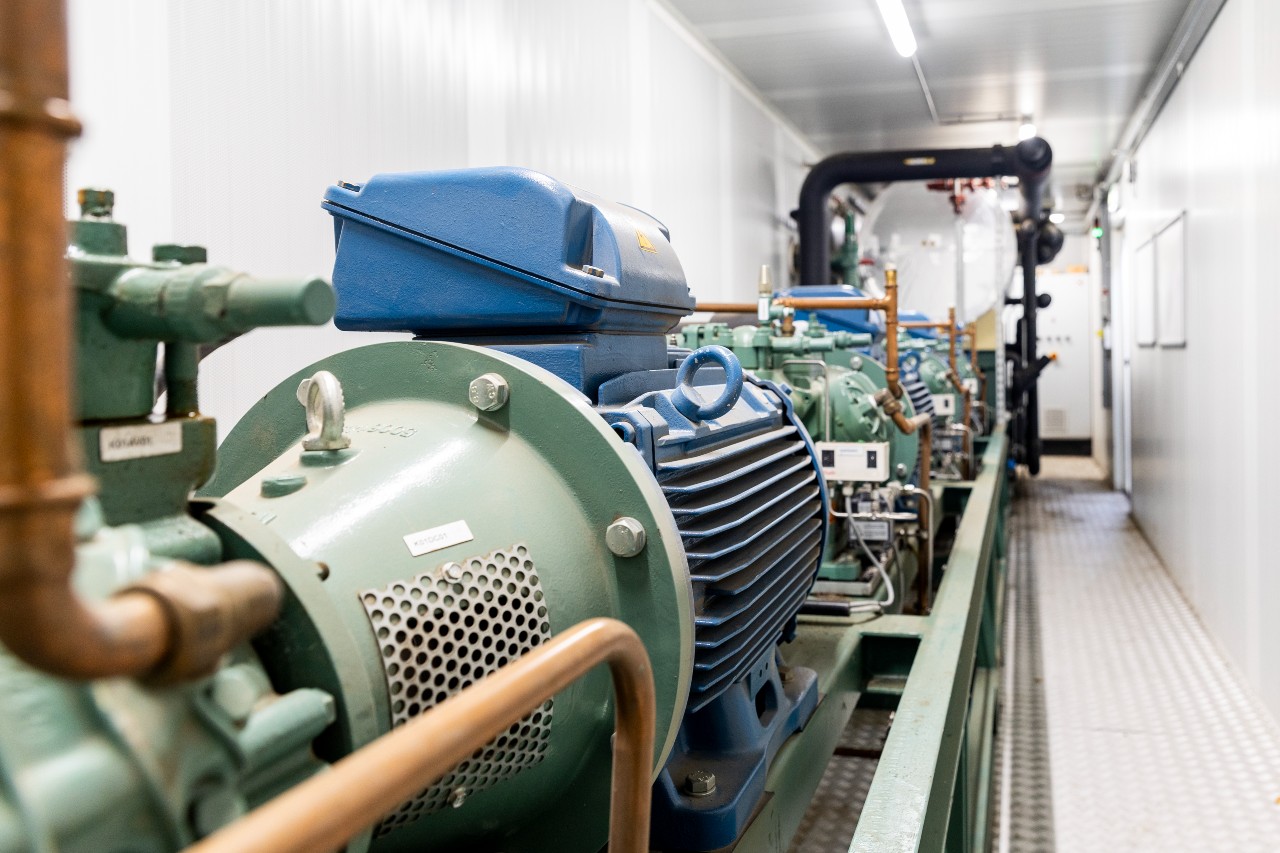
In a drop-in, R22 is removed and replaced with an alternative refrigerant or topped-up with an alternative refrigerant. This scenario is suitable for installations that are less than 10 years old and are already prepared to use a synthetic refrigerant. Disadvantages of a drop-in include reduced cooling capacity, increased energy consumption and shortened life of the system. In many cases, therefore, a drop-in is less suitable as a permanent solution.
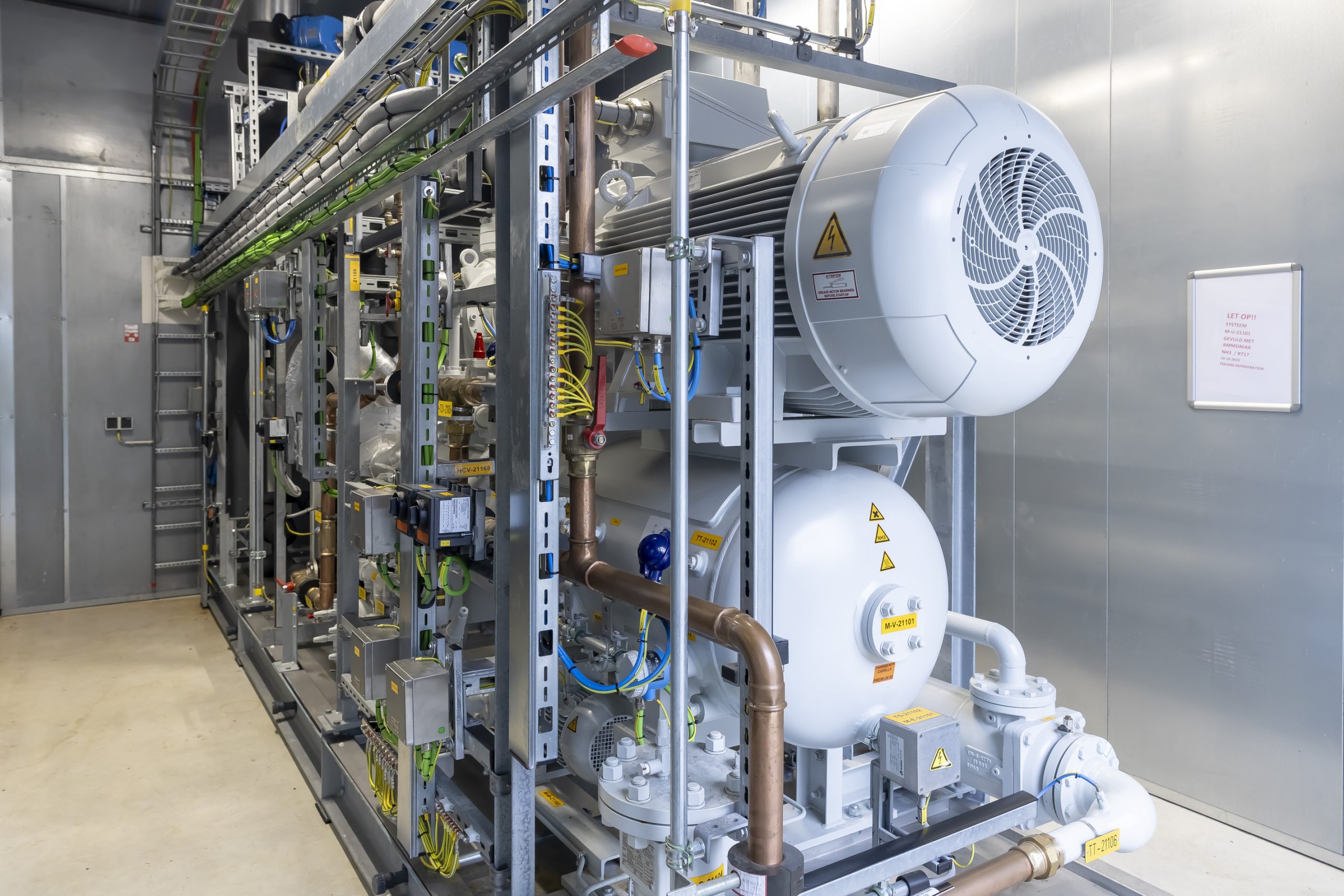
It is possible to make your R22 installation suitable for an alternative refrigerant. This involves replacing a number of components to allow natural refrigerant cooling. This scenario fits large, well-maintained industrial cooling installations, for example, installations in the shipping industry. When adapted, they can last for years, making early and high cost investments unnecessary.
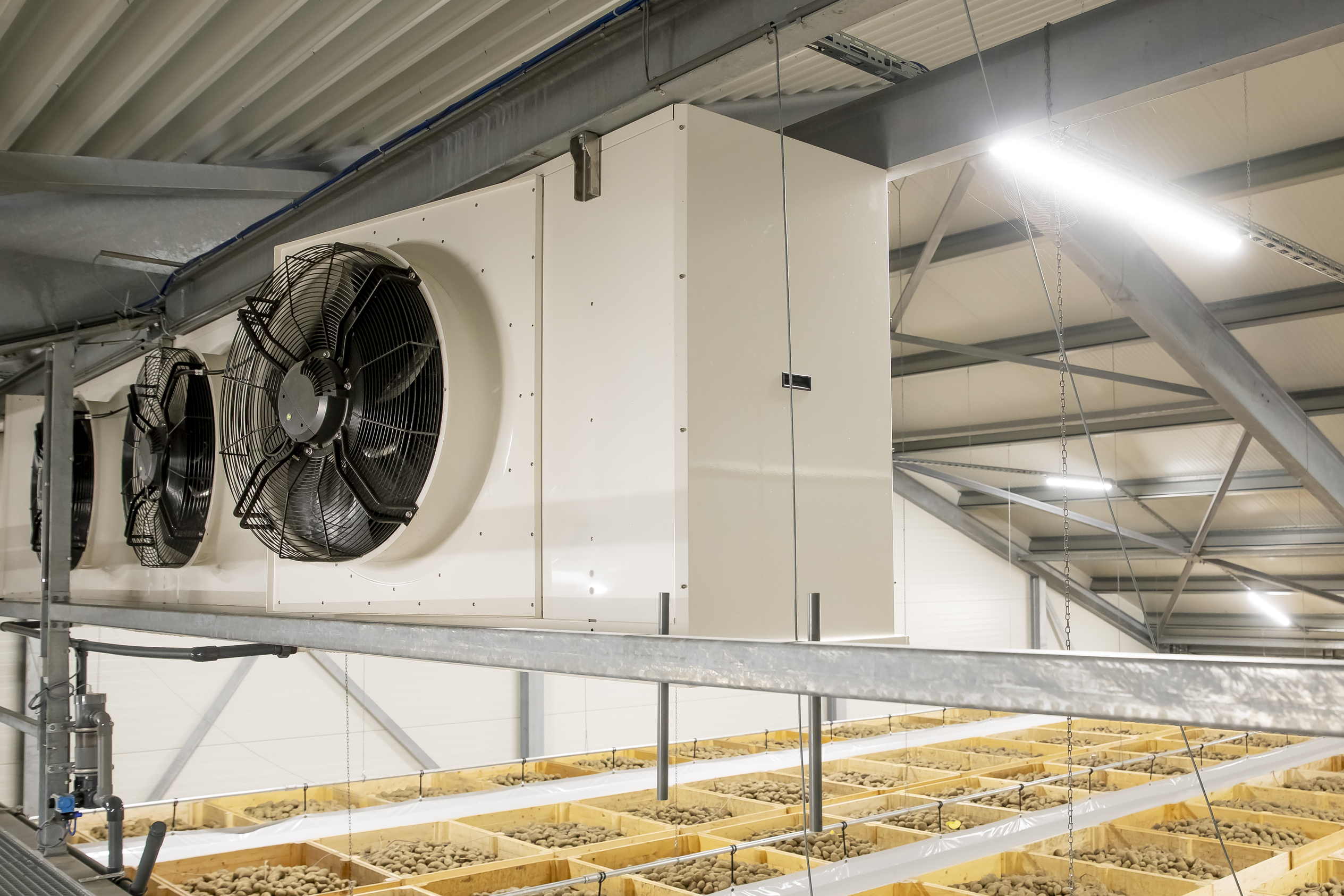
Replacing R22 by natural refrigerants in your cooling installation is a sustainable solution. Increasingly, more installations run on natural refrigerants, such as CO2, propane, or ammonia. These solutions are environmentally friendly and very energy efficient. With this, you also comply with legislation in the long term and as an entrepreneur, you can benefit from lucrative tax schemes. Various entrepreneurs have achieved considerable financial savings with this.
Monitoring and enforcement
Remember that the authorities may visit your company to inspect the R22 refrigeration system. The Human Environment and Transport Inspectorate (ILT) of the Ministry of Infrastructure and Water Management monitors compliance with the legislation. It visits companies with R22 refrigeration systems to check compliance with the statutory leakage checks. The ILT also checks the refilling and replenishing of R22 systems. You are required by law to cooperate with ILT inspections.
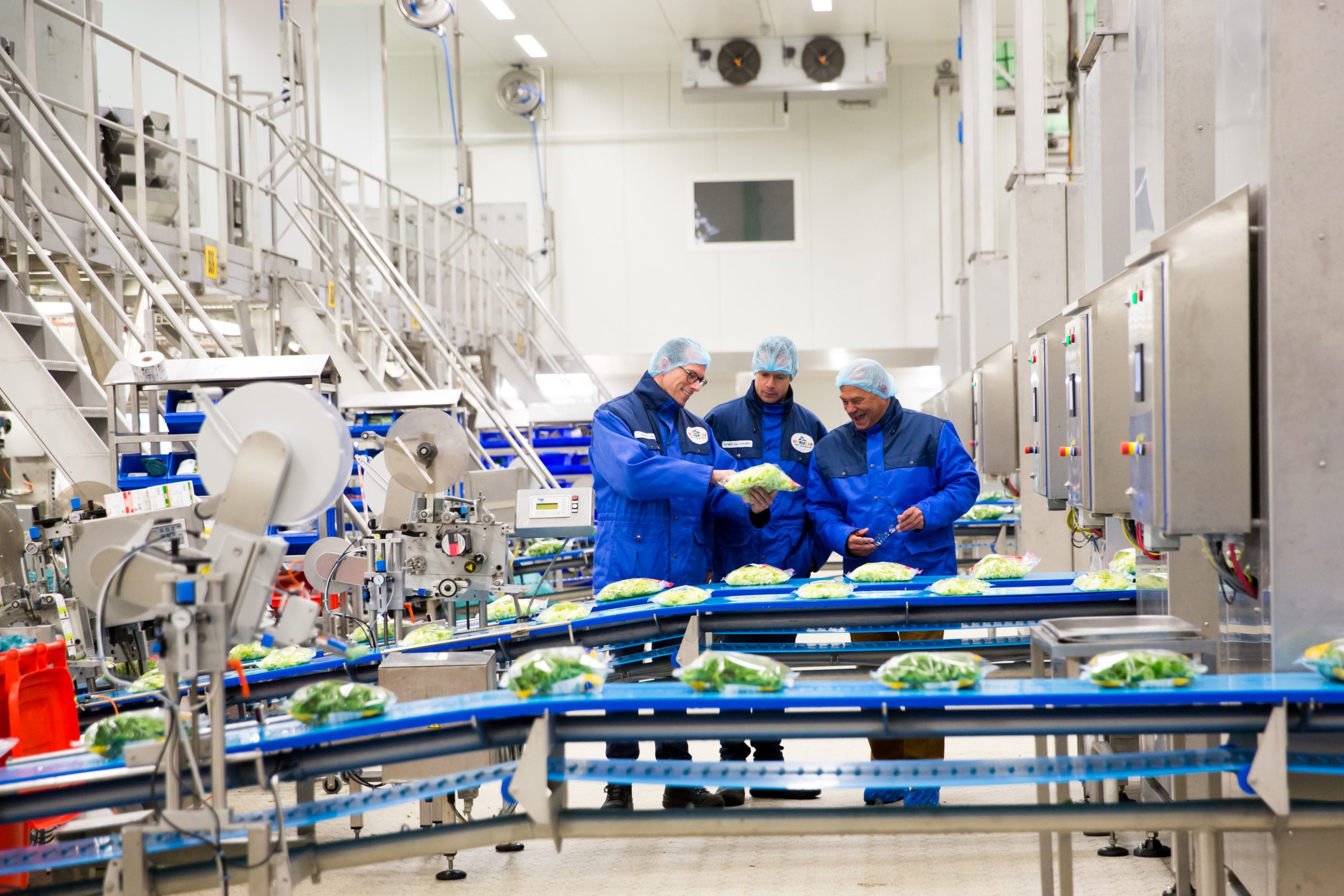
Are you curious about how our natural refrigerant cooling technology works in practice every day? Then read the Heemskerk fresh & easy case study. For this vegetable processing company, we replaced the Freon refrigeration system with a refrigeration system using ammonia as the refrigerant, and CO2 and glycol as the coolant. The result: doubled cooling capacity and significant energy savings.